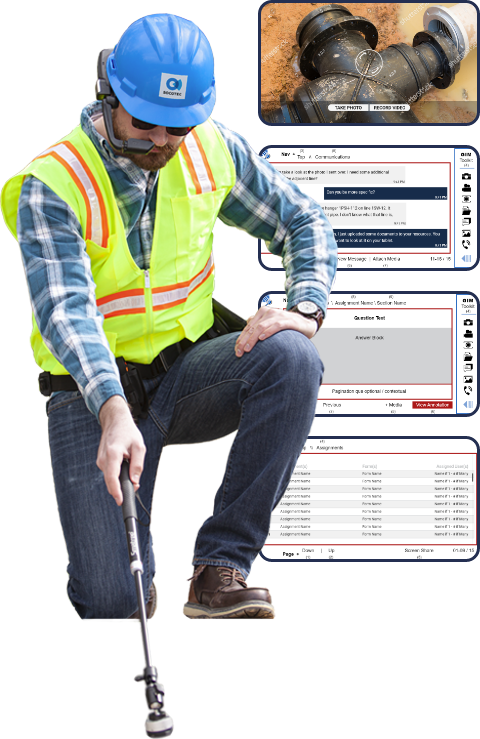
Efficient Field Inspections
The WISE-BACK™ inspection system offers a streamlined, customized approach to data collection that runs across multiple devices. Capture photos and videos using the tools that provide the best perspective and annotate them in the field while that information is directly in front of you.
Voice-activated controls allow freedom of movement, keeping users on focus, on task. The tool belt comes complete with integrated inspection tools to get the job done in less time. The flexible user interface is comprised of a headset, tablet and smartphone that allows the user to enter data by voice, keyboard, or stylus.
Field users can reach out to remote experts in real time for guidance and review, reducing excursions.
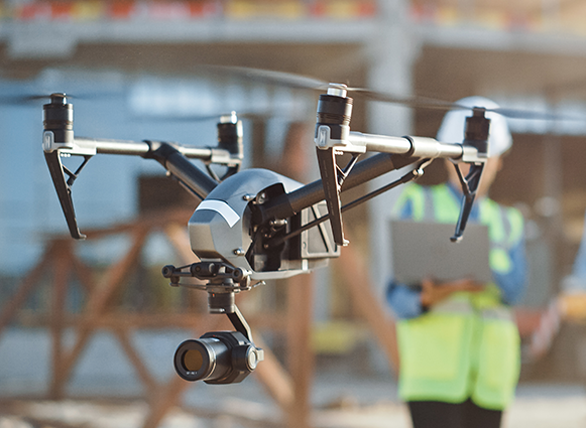
Force Multiplier
Leverage your inhouse expertise with WISE-BACK™. Using voice and video communications, offsite remote experts can get real-time field perspectives and data to assist the field user. Troubleshoot complex problems remotely, supply resources and receive additional details in real time.
Base Station users can actively participate in a number of field activities occurring simultaneously at different locations, providing expertise, guidance or review as needed without the sheer cost and lost time of travel.
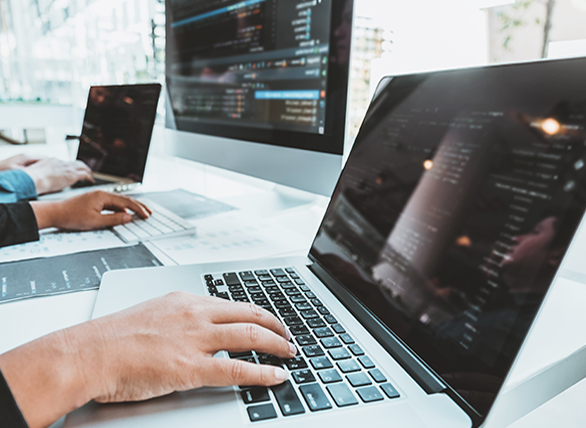
Enhanced Safety
When inspecting difficult or hazardous locations is part of the job, safety is a high priority. Reducing the number of excursions is by far the best and most cost-effective way to increase safety. Often data analyzed with a team after the fact is incomplete and requires multiple inspections to gain a complete picture. WISE-BACK™ empowers field technicians. Communicate via voice-activated video with the control room and site personnel, leverage offsite team members on the fly, share and mark up media in real time to assist in communication and ensure understanding is concordant before leaving a difficult area.
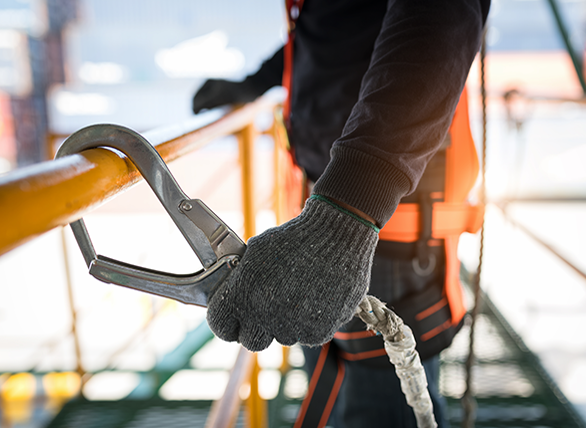
Preventive Maintenance
Maintenance activities from oil changes to overhauls are performed more quickly, reliably and safely thanks to WISE-BACK™. The WISE-BACK™ system can bring a library of documents—from maintenance manuals to 3D models—to the job site for display on a headset, tablet or smartphone. Procedures and checklists can be displayed one step at a time on the headset display and augmented by photos and drawings. On-line chats enable consultation with equipment experts and peer reviewers, giving them real-time views of the work being performed and the ability to provide guidance. Voice confirmation, audio notes and media capture provide high-quality documentation of the activities faster and more accurately than pen and paper.
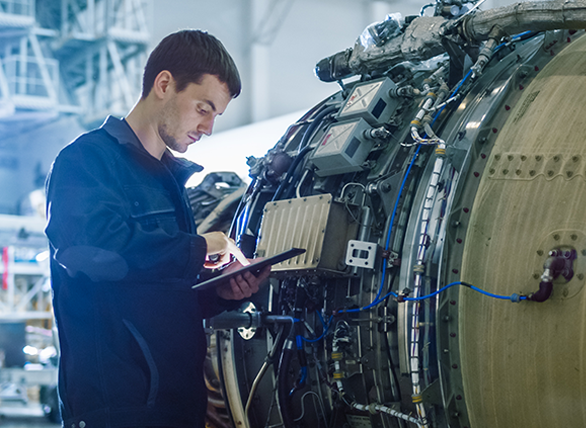
Proactive Opportunities
It’s not uncommon for plant engineers to observe equipment aging issues—leaks and spills, damaged or degraded equipment, inoperable components—while engaged in totally unrelated activities. Use WISE-BACK™ to notify the control room for immediate action and provide images, videos and measurements. If the situation is less urgent, use captured media to identify and track potential issues for later evaluation and addition to an action items list. Quickly log casual observations in a searchable and indexable format. WISE-BACK™ prevents potentially high-impact issues from being found and then forgotten.
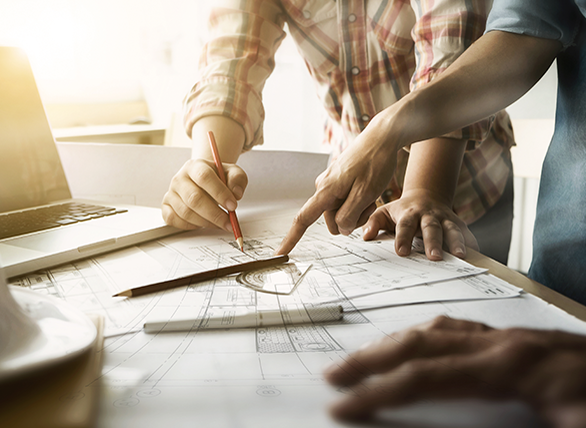
Training
WISE-BACK™ allows training and mentoring of staff at different locations in real time. Course correct new recruits during an exercise, or capture video from the trainee’s perspective for later review with instructors. Assignment-based live testing and validation reduces the learning-feedback back loop, ensuring efficiency in training.
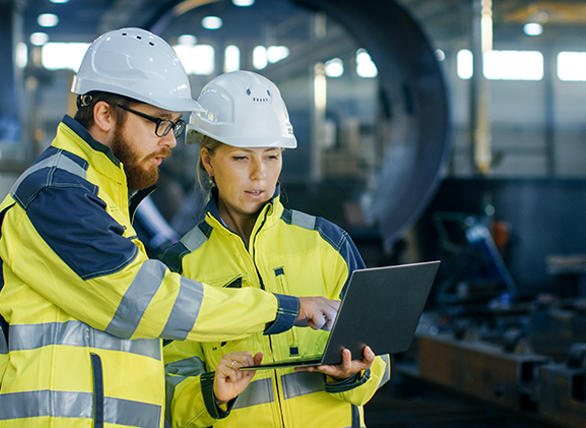